30V 350mA Step-down HB LED Driver PT4211
Crmicro-PT4211_English_Datasheet.pdf
PT4211 GENERAL DESCRIPTION
The PT4211 is a continuous conduction mode inductive step-down converter,designed for driving single or multiple series connected LEDs from a voltage source higher than the LED voltage. The device operates from an input supply between 5V and 30V and provides an externally adjustable output current of up to 350mA.The PT4211 includes the output switch and a high-side output current sensing circuit, which uses an external resistor to set the nominal average output current, and a dedicated DIM input accepts a wide range of pulsed dimming. Applying a voltage of 0.4V or lower to the DIM pin turns the output off and switches the device into a low current standby state. Built-in Soft Over Temperature Protection protects the device from over temperature damage.
The PT4211 is available in SOT23-5 package.
PT4211 FEATURES
●Simple low parts count
●Wide input voltage range: 5V to 30V
●Up to 350mA output current
●PWM dimming
●3% output current accuracy.
●Up to 1MHz switching frequency
●Typical 3% output current accuracy
●Inherent open-circuit LED protection
●High efficiency (up to 93%)
●Adjustable Constant LED Current
●High-Side Current Sense
●Hysteretic Control: No Compensation
●Soft Over Temperature Protection
PT4211 APPLICATION
●Low voltage halogen replacement LEDs
●Automotive lighting
●LED back-up lighting
●Illuminated signs
PT4211 ORDERING INFORMATION
PACKAGE
| TEMPERATURE RANGE | ORDERING PART NUMBER | TRANSPORT MEDIA | MARKING
|
SOT23-5
| -40℃ to 85℃ | PT4211E23E
| Tape and Reel 3000 units | 4211 xxxxxX |
PT4211 TYPICAL APPLICATION CIRCUIT
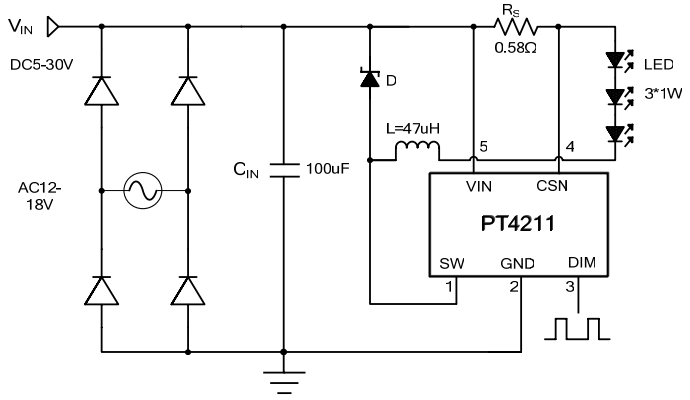
PT4211 PIN ASSIGNMENT
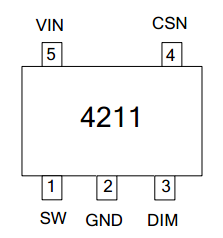
PT4211 OPERATION DESCRIPTION
The device, in conjunction with the coil (L) and current sense resistor (RS), forms a self oscillating continuous-mode buck converter.
When input voltage VIN is first applied, the initial current in L and RS is zero and there is no output from the current sense circuit. Under this condition, the output of CS comparator is high. This turns on the internal switch and switches the SW pin low, causing current to flow from VIN to ground, via RS, L and the LED(s). The current rises at a rate determined by VIN and L to produce a voltage ramp (VCSN) across RS. When (VIN-VCSN) > 230mV, the output of CS comparator switches low and the switch turns off. The current flowing on the RS decreases at another rate. When (VIN-VCSN) < 170mV, the switch turns on again and the mean current on the LED is determined by
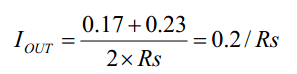
The high-side current-sensing scheme and on-board current-setting circuitry minimize the number of external components while delivering LED current with ±3% accuracy, using a 1% sense resistor.
The PT4211 allows dimming with a PWM signal at the DIM input. A logic level below 0.4V at DIM forces PT4211 to turn off and the logic level at DIM higher than 1.7V to turn the device on. The frequency of PWM dimming ranges from 100Hz to more than 20 kHz.
The DIM pin is pulled up to the internal 5V by a resistor when it is floating. When a voltage applied to DIM falls below the threshold (0.4V nom.), the switch is turned off. The internal regulator and voltage reference remain powered during shutdown to provide the reference for the shutdown circuit. Quiescent supply current during shutdown is nominally 95uA and switch leakage is below 5uA.
Additionally, to ensure the reliability, the PT4211 is built with a thermal shutdown(TSD) protection. The TSD protests the IC from over temperature, when junction temperature more than 135℃ the output current begins to decrease until to zero at 150℃.
PT4211 APPLICATION NOTES
Setting nominal average output current with external resistor RS
The nominal average output current is determined by the value of the external current sense resistor (RS) connected between VIN and CSN and is given by: :
IOUT=0.2/Rs(Rs≥0.17Ω)
This equation is valid when DIM pin is logic high.
Output current adjustment by PWM control
A Pulse Width Modulated(PWM) signal with duty cycle PWM can be applied to the DIM pin, as shown below, to adjust the output current to a value below the nominal average value set by resistor RS:
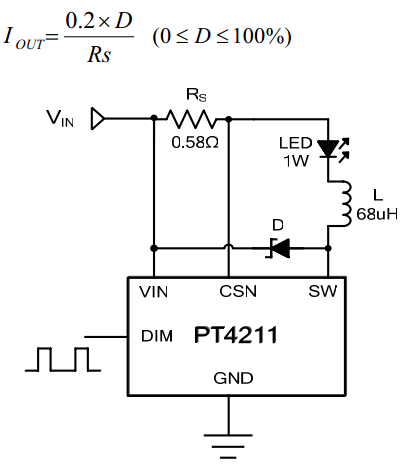
PWM dimming provides reduced brightness by modulating the LED’s forward current between 0% and 100%. The LED brightness is controlled by adjusting the relative ratios of the on time to the PWM signal cycle time. A 25% brightness level is achieved by turning the LED on at full current for 25% of one cycle. To ensure this switching process between on and off state is invisible by human eyes, the switching frequency must be greater than 100 Hz. Above 100Hz, the human eyes average the on and off times, seeing only an effective brightness that is proportional to the LED’s on-time duty cycle. The advantage of PWM dimming is that the forward current is constant; therefore the LED color does not vary with brightness as it does with analog dimming. Pulsing the current provides precise brightness control while preserving the color purity. The dimming frequency of PT4211 isdepending on the operating frequency. To achieve the best dimming linearity, the dimming frequency is recommended to limited less than 1% of operating frequency.
Shutdown mode
Taking the DIM pin to a voltage below 0.4V will turn off the output and the supply current will fall to a low standby level of 95μA nominal.
Inherent open-circuit LED protection
If the connection to the LED(s) is open-circuited, the coil is isolated from the SW pin of the chip, so the device and LED will not be damaged. When the LED(s) load is connected the device will enter normal operation.
Capacitor selection
A low ESR capacitor should be used for input decoupling, as the ESR of this capacitor appears in series with the supply source impedance and lowers overall efficiency. This capacitor has to supply the relatively high peak current to the coil and smooth the current ripple on the input supply. A minimum value of 4.7uF is acceptable if the DC input source is close to the device, but higher values will improve performance at lower input voltages, especially when the source impedance is high. For the rectified AC input, the capacitor should be higher than 100uF and the tantalum capacitor is recommended. The input capacitor should be placed as close as possible to the IC.
For maximum stability over temperature and voltage, capacitors with X7R, X5R, or better dielectric are recommended. Capacitors with Y5V dielectric are not suitable for decoupling in this application and should NOT be used. A suitable Murata capacitor would be GRM42-2X7R475K-50.
Inductor selection
Recommended inductor values for the PT4211 are in the range 47uH to 100uH. Higher values of inductance are recommended at lower output current in order to minimize errors due to switching delays, which result in increased ripple and lower efficiency. Higher values of inductance also result in a smaller change in output current over the supply voltage range. (See graphs). The inductor should be mounted as close to the device as possible with low resistance connections to the SW and VIN pins. The chosen coil should have a saturation current higher than the peak output current and a continuous currentrating above the required mean output current. Following table gives the guideline on inductor selection:
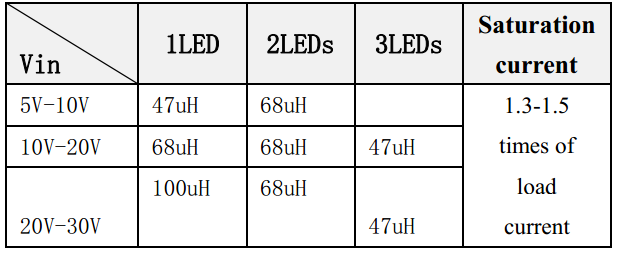
Suitable coils for use with the PT4211 are listed in the table below:
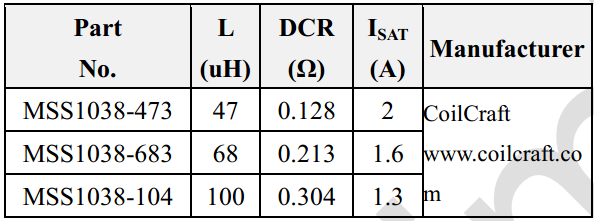
The inductor value should be chosen to maintain operating duty cycle and switch 'on'/'off' times within the specified limits over the supply voltage and load current range.
Diode selection
For maximum efficiency and performance, the rectifier(D) should be a fast low capacitance Schottky diode with low reverse leakage at the maximum operating voltage and temperature.
They also provide better efficiency than silicon diodes, due to a combination of lower forward voltage and reduced recovery time.
It is important to select parts with a peak current rating above the peak coil current and a continuous current rating higher than the maximum output load current. It is very important to consider the reverse leakage of the diode when operating above 85°C. Excess leakage will increase the power dissipation in the device and if close to the load may create a thermal runaway condition. The higher forward voltage and overshoot due to reverse recovery time in silicon diodes will increase the peak voltage on the SW output. If a silicon diode is used, care should be taken to ensure that the total voltage appearing on the SW pin including supply ripple, does not exceed the specified maximum value. The following web sites are useful when finding alternatives: www.onsemi.com
Reducing output ripple
Peak to peak ripple current in the LED(s) can be reduced, if required, by shunting a capacitor CLED across the LED(s) as shown below:
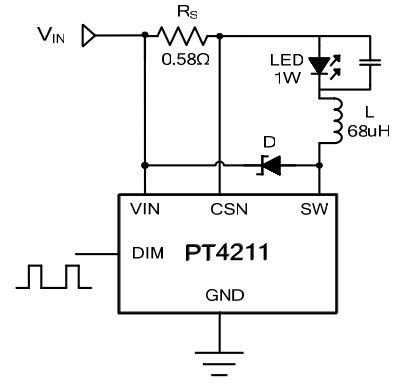
A value of 1uF will reduce the supply ripple current by a factor three (approx.). Proportionally lower ripple can be achieved with higher capacitor values. Note that the capacitor will not affect operating frequency or efficiency, but it will increase start-up delay and reduce the frequency of dimming, by reducing the rate of rise of LED voltage.
Operation at low supply voltage
With the supply voltage below the output voltage, the switch duty cycle will be high and the device power dissipation will be at a maximum. Care should be taken to avoid operating the device under such conditions in the application, in order to minimize the risk of exceeding the maximum allowed die temperature.